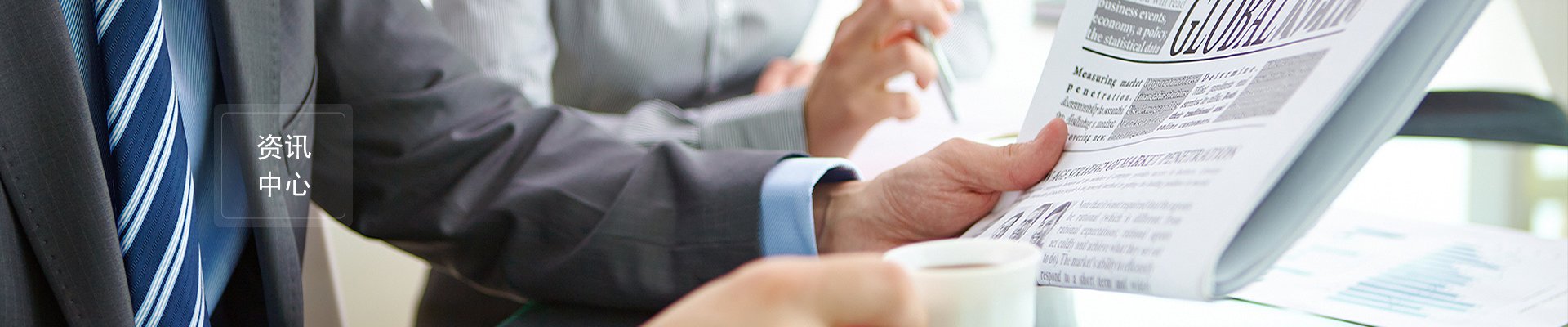
光学镜头的结构设计与装配工艺
发布时间:2020年12月05日
光学冷加工:
很多没进过光学冷加工车间的朋友对光学透镜的加工技术很好奇,今天我们大致说说,其实光学冷加工就是把像石头一样形状的光学玻璃原料,进行切割,粗磨,精磨,抛光,磨边,镀膜,胶合等一整套工艺,最终得到图纸要求精度的光学透镜。
具体的光学冷加工工艺在这里就不详细说了,此处重点说一下目前国内光学透镜的一般加工精度:
1.外径公差-0.02~0左右;
2.中心厚度公差:±0.02左右;
3.偏心:2′左右;
4.光圈:3左右;
5.局部光圈:0.3左右;
6.镀增透膜后的反射率:小于0.5%左右。
注:光学透镜的标注是需要进行严格的公差分析的,此处给出的是一般的加工精度,只作为参考。另外,需要注意的是,公差标注的越紧,加工难度就越大,车间的报废率就会越高,对于需要考虑成本的镜头来说,这个是需要结合公差分析的结果,仔细权衡的。
结构设计
1.参照该装配图,改镜头主要分为前组,中一组,前压帽,中二组,后组,隔圈,镜体,物镜壳,压圈,弹簧,后光栏等几个零件。
2.本设计共有5片透镜,第一片透镜固定在前组里,第二片和第三片透镜胶合在一起,固定在中一组里,第四片透镜固定在中二组里,第五片透镜固定在后组里。
3.前组,中一组,中二组,后组,隔圈是放在镜体里面的,然后用压圈压住,而镜体的外面旋有物镜壳和前压帽。镜体和物镜壳之间装有弹簧(保护样品),后光栏旋在物镜壳内。
4.肯定有人要问:为什么要把镜片固定在前组,中一组,中二组和后组里,而不是直接放在镜体里?那是因为,采用前者的方式,可以得到更高的同轴精度,它是采用光学中心仪,先确定前组机械轴(对前组的机械加工要求很高,需要“一刀切”),然后移动透镜,使得透镜的光轴与前组机械轴共轴,再点胶,曝光,固定。
5.前组,中一组,后组和镜体的配合间隙越小越好,前组,中一组,后组外径公差和镜体内径公差可以标注在5um左右。
6.中二组和镜体的间隙大概有0.1到0.2左右,目的是留有调节彗差的余量。
7.前组,中一组,中二组,后组,隔圈内部车有螺纹(遮光丝),目的是减少杂散光。
装配工艺
对于该镜头来说,装配镜头的过程就是调节像差(球差,彗差,象散,场曲,畸变,两种色差)的过程,此处主要介绍工厂里常用的“星点法”。
星点法是用透射光照在一个镀有铝膜的玻璃板上(铝膜很薄,有些部分会透光),产生衍射斑,然后通过带有需要调校镜头的显微系统观察。理论上,如果该镜头没有像差,那么在目镜视野里看到的衍射斑点都应该是艾里斑加几个很细的圆环,所以调校镜头的过程是一边观察衍射斑形状一边改变镜头参数的实时过程。对于拥有丰富调校镜头经验的老师傅来说,他们一眼就可以看出来镜头存在哪一种像差,该如何调校。对于刚入门的新手来说,这个是相当困难的,本屌丝刚毕业时曾经在车间花了1个月的时间学习擦拭玻璃,最终是勉强通过师傅的考核,至于观察衍射斑的形状,并与各种像差一一对应则是花了3个月的时间,最终也才是略知皮毛。
实践的过程只能亲身体验,不好言传,下面对衍射斑的形状和各种像差的对应做一个小结:
1.球差:艾里斑亮度占整个衍射斑的的亮度比例不对(理论上是84%)或者衍射环太粗;一般的解决方法是通过车削镜座或者在镜座之间加垫片来改变空气间隔(需要用软件模拟各个空气间隔的敏感程度,再决定在镜头的什么位置进行变动);
2.彗差:顾名思义,就是衍射斑像彗星尾巴的形状;一般的解决方法是调整同轴度,上面提到的“中二组和镜体的间隙大概有0.1到0.2左右”正是这个目的,另外,需要注意的是,镜头刚装配好,彗差往往是最明显的,所以一般都是调整同轴度,校正彗差,然后再观察其他几种像差。
3.象散:需要旋转镜头观察,一般通过更换玻璃来改善(象散难以调节的镜头往往是镜头里面某些玻璃的面型超差);
4.场曲:离焦观察中心视野与边缘视野的斑点情况;
5.畸变:衍射斑点形状不规则,如果不是设计本身的问题,此种异常往往也是需要从透镜的面型下手。